The climate crisis is a critical area of concern for governments, businesses and individuals worldwide. The urgent need for action is made clear when considering rising temperatures, extreme weather events and food and water insecurity. The Paris Agreement of 2015 set warming limits to below 2°C, and ideally 1.5°C, to avoid catastrophic impacts of climate change. Since that agreement, governments have reconfirmed the importance of this, such as at the COP26 summit in Glasgow in November 2021. Here, world leaders committed to significantly reducing carbon dioxide and methane fugitive emissions. The valve industries have an essential role to play.
What Are Fugitive Emissions?
Fugitive emissions are the unintentional and undesirable emission, leakage, or discharge of gases or vapours from components inside an industrial plant such as valves, piping flanges, pumps, storage tanks and compressors. The term “fugitive” is used because these emissions are not taken into account and calculated during the design of the equipment and components. In addition, these emissions are unanticipated. Unlike smokestack emissions, which are released through a controlled channel, fugitive emissions escape into the atmosphere in an irregular and diffuse way. This makes them difficult to track and quantify, and as such, they are not detected by typical monitoring and control devices. Since typical control equipment and facilities cannot detect them, fugitive emissions can also be called uncontrolled or unanticipated emissions.
Although individual leaks may seem small, collectively they contribute significantly to air pollution and climate change, with estimates suggesting that they account for around 5% of global GHG emissions.
Methane is the primary fugitive emission from the oil, gas and chemical industries. By volume, methane sits behind carbon dioxide but it has a disproportionate impact on the environment due to its high global warming potential. It is 28 times more potent than carbon dioxide. Preventing unwanted methane emissions has therefore become increasingly important to facilities as its detrimental effects are apparent.
Mitigating Fugitive Emissions
The fight against climate change necessitates stricter regulations on industrial emissions. Fugitive emissions, particularly methane leaks from valves, are a major environmental concern. Fortunately, metal valve seals can contribute to compliance with these regulations.
Here are some key regulations that metal valve seals can help address:
The Environment Agency (EA) Regulations: The Environment Agency enforces regulations to minimise some fugitive emissions in the UK. The primary international standards for reducing industrial fugitive emissions are defined by the American Petroleum Institute standard API 641 and International Organisation for Standardisation ISO 15848.
BS EN 1591-1:2013: This British Standard outlines that metal valve seals can be very effective in these areas. By implementing metal valve seals, facilities demonstrate their commitment to best practices and responsible environmental management.
Using metal valve seals not only benefits the environment, but also helps companies avoid potential fines and penalties associated with non-compliance.
Why Traditional Valve Sealing Materials Fall Short
Traditionally, valves have relied on soft, compressible materials like graphite or PTFE packing for sealing. While these materials offer good initial sealing performance, they have limitations:
- Temperature Sensitivity: These types of valve seals struggle in extreme environments, becoming hard and brittle at cryogenic temperatures and losing effectiveness above 250°C (482°F).
- Porosity: These materials have inherent porosity, allowing for small gas leaks over time.
These limitations become especially problematic as industrial processes push the boundaries with ever-increasing pressures and temperatures.
Fugitive Emissions from valves
Statistics show that about 60% of methane fugitive emissions come from valves, and up to 80% of these leakages are from stem-seal interfaces. Approximately 10,000 to 15,000 valves may exist in a typical refinery. This reinforces valves as a key concern, playing a vital role in preventing fugitive emissions.
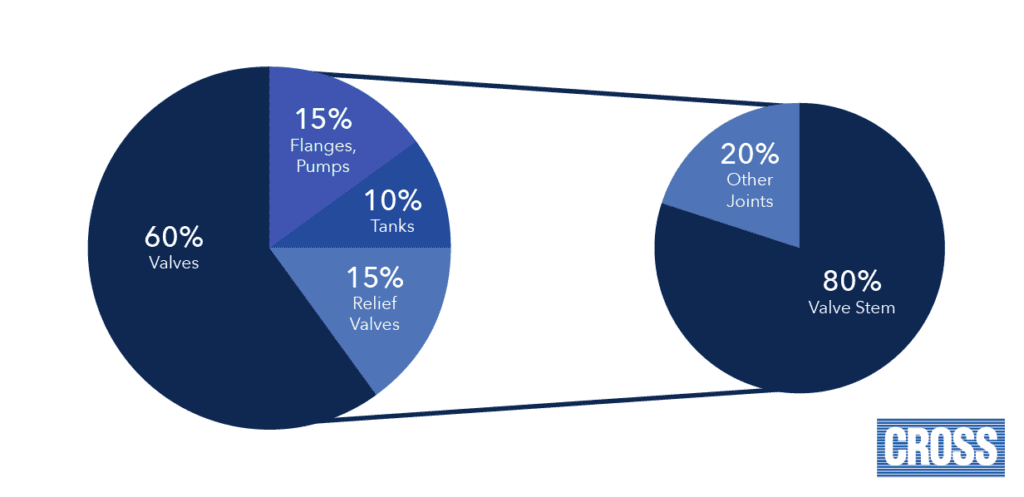
Also contributing to valve failures are leaks at the bonnet, flanges and seats. As operating conditions in these and other industries continue to subject valves to ever more extreme temperatures and pressures, sealing them effectively poses a challenge that cannot be met with traditional materials and methods. Soft, compressible elastomers provide good sealing performance, but as they are porous, they cannot withstand temperatures in excess of 250°C (482ºF). They also become hard and brittle in cryogenic service. Metal seals have much greater temperature capabilities, high mechanical properties, lack of porosity and long shelf life.
Valve stems, which as noted are the single largest source of fugitive emissions, continue to be sealed with graphite or PTFE compression packing. However, neither of these materials is suitable for cryogenic or high-temperature service in the presence of oxygen. Spring-energised metal seals for rotary, rising stem and linear valves can provide full metal-to-metal contact, leak tightness and accommodation of axial stem movement. Also available for sealing valve stems are special ring sets that control fugitive emissions and withstand the severe conditions of service in chemical, petrochemical and nuclear facilities.
Today these more resilient, metal-to-metal seals are available and being used in valves operating under extreme conditions. Metal seals are used where other materials are unacceptable. Manufactured in a wide range of sizes, they provide infinite storage life and long-term sealing with no porosity. These properties make them the sealing solution of choice for valves operating in today’s increasingly extreme environments.
The Economic Advantages of Metal Valve Seals
The benefits of metal valve seals extend beyond environmental improvements. They can offer significant economic advantages compared to traditional packing materials:
Reduced Maintenance Costs
Metal seals require less maintenance due to their durability and extended lifespan. This translates to significant labour cost savings compared to the frequent maintenance which may be needed for traditional packing.
Extended Seal Life
Unlike compressible packing that degrades over time, metal seals offer long-lasting performance, minimising the need for replacements and downtime.
Improved Energy Efficiency
Leak-tight metal seals can also improve the efficiency of plant operations leading to cost savings through reduced energy consumption required for plant operations.
By considering these factors, a switch to metal valve seals can present a compelling return on investment (ROI). The initial investment is often offset by reduced maintenance costs, extended seal life, and energy savings.
Contact us today
Our dedicated customer service teams are waiting to hear from you. To reach the right team please give us brief details and press submit.
You can also call our main office line on +44 (0)3301 224 400.