In this article, we outline the types of turbo compressor and their applications and take a deeper dive into the turbocharger explaining why it’s different.
What is a turbo compressor?
Turbo compressors are a type of Turbomachinery of which there are two main categories; those which are primarily used to produce power, such as gas turbines used in the power generation industry, or aircraft engines used to provide thrust, and those that typically consume power to increase the pressure of a fluid or gas, which includes compressors, pumps, and fans.
Turbo compressors usually work with gas and are further categorised by their flow type. When the flow is parallel to the axis of rotation, they are called axial flow compressors, producing a compressed column of gas.
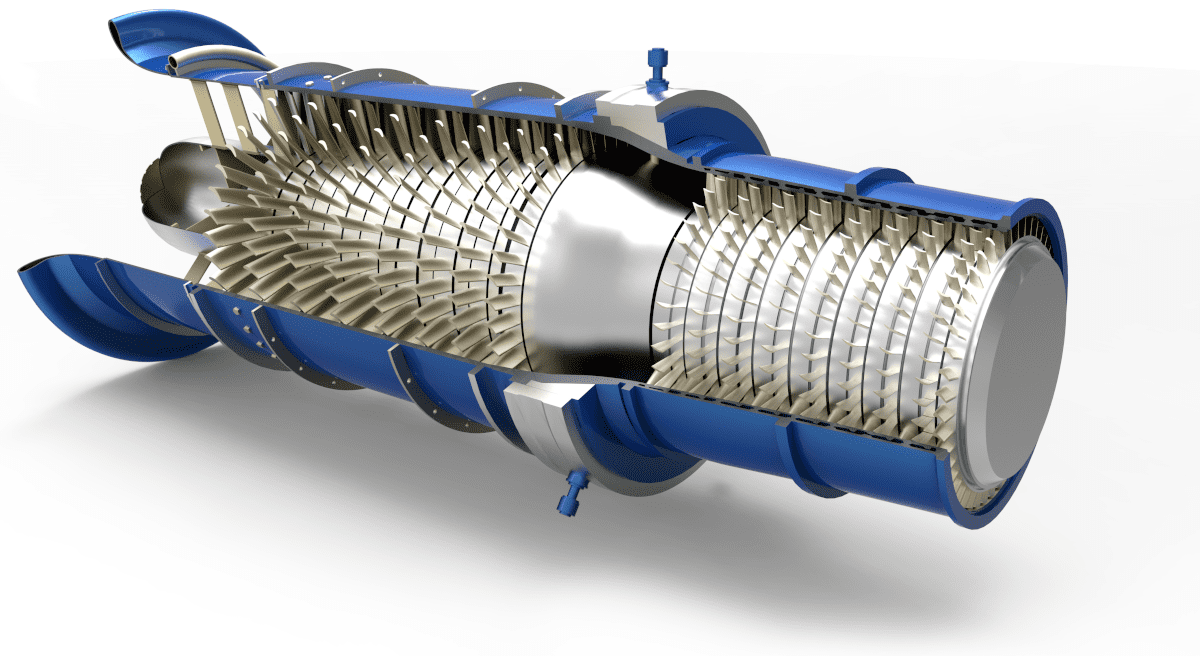
When flow is perpendicular to the axis, they are referred to as radial (or centrifugal) compressors where the gas is forced to the outside using centrifugal force. There are also mixed flow compressors which combine axial and radial components to produce a diagonal flow.
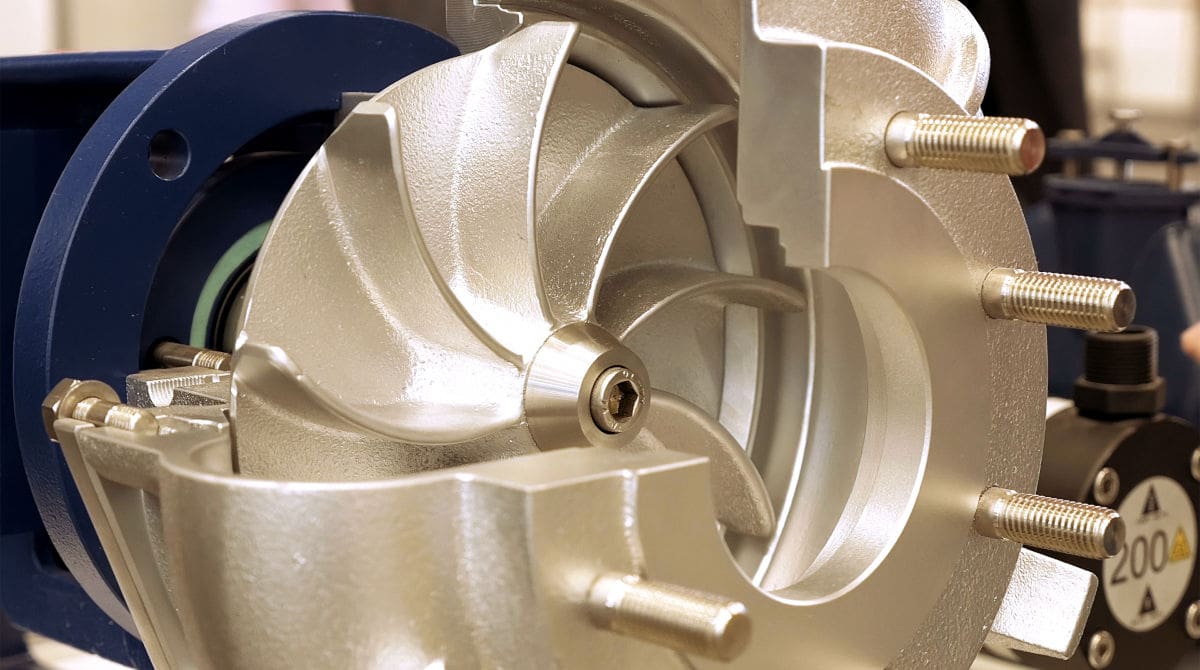
What is the difference between a turbo compressor and a turbocharger?
A turbocharger is a type of turbo compressor, a centrifugal compressor with its flow perpendicular to the axis of rotation.
The main difference between a turbocharger and other types of turbo compressor is that a turbocharger is powered by waste exhaust gases flowing through its turbine wheel rather than receiving power from another source, such as an electric motor, belt driven from an internal combustion engine, or from direct fuel combustion as within a gas turbine compressor.
How does a turbocharger work?
As already mentioned, a turbocharger is a centrifugal compressor, comprising of a turbine wheel connected to a compressor wheel by a shaft. It is mounted in the exhaust system between the manifold and exhaust pipe.
As the waste exhaust gas exits the engine, it drives the turbine wheel which turns the compressor wheel at the other end of the shaft. The exhaust gas then leaves via the exhaust pipe. Meanwhile, the compressor wheel sucks in air, compressing it and forcing it into the engine, usually via an intercooler, improving the performance and fuel consumption.
As the waste gases are expelled from the engine, they are directed through the turbocharger turbine wheel and so completes the cycle.
Read more about the sustainable future of turbochargers.
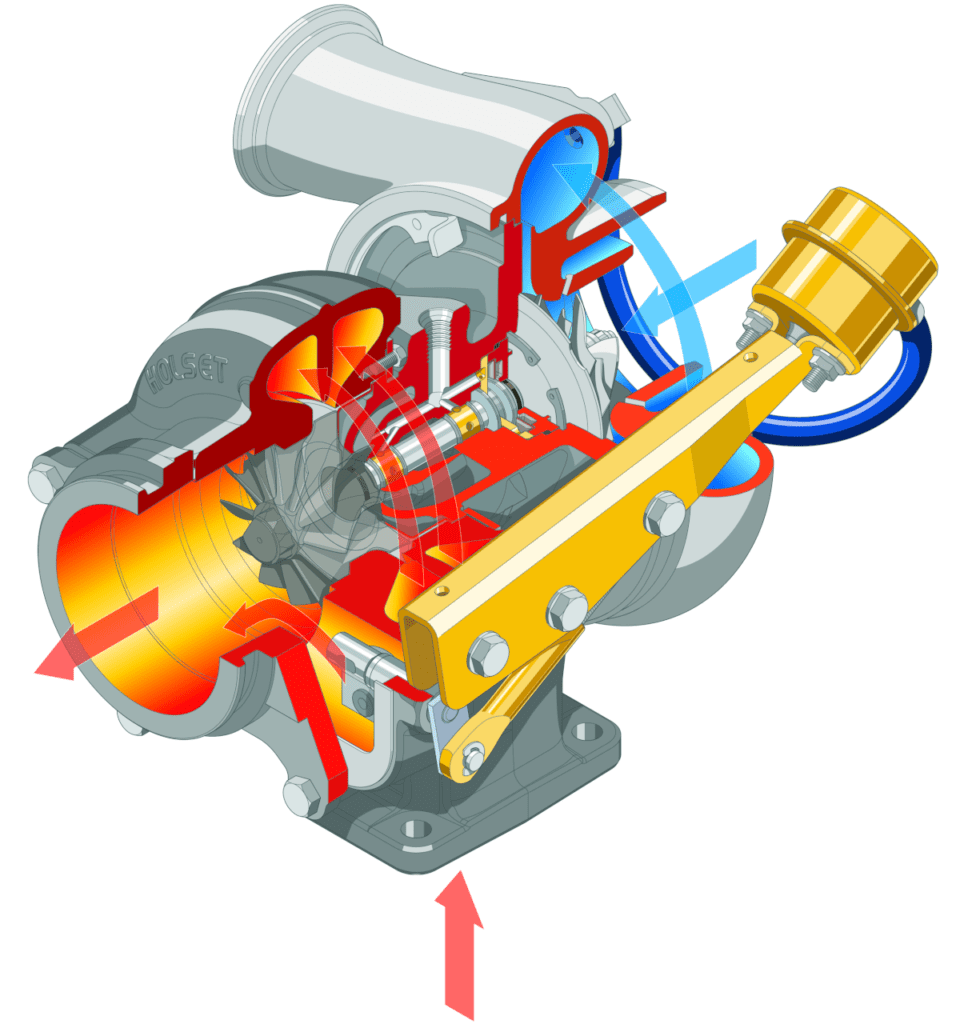
How have turbochargers been used historically?
From the development of the world’s first turbochargers in the early 1900s, through to the fuel crisis and introduction of strict fume emission regulations, modern turbochargers now reduce fuel consumption and fume emissions alongside improving the efficiency of internal combustion engines (ICEs).
Prior to the 1980s, turbochargers (or centrifugal turbo compressors) were reserved for large engines, such as in ships, locomotives, and aircrafts. However, turbocharged engines were then introduced into domestic vehicles. During the 1980s, Mercedes and Volkswagen both introduced turbocharged engines into a series of diesel vehicles. Most modern ICE engines are fitted with turbochargers, and therefore have much higher efficiency.
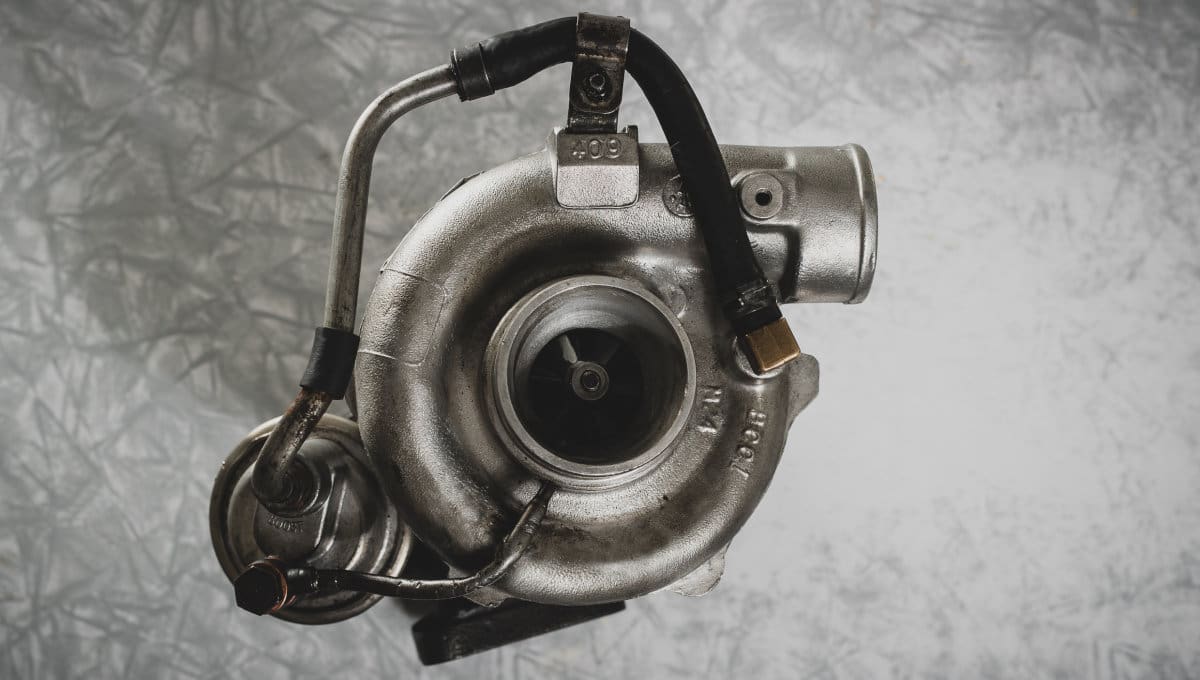
Where are turbo compressors used?
Turbo compressors are used for many different applications, such as compressed air for pneumatic tools, in refrigeration, air-conditioning and HVAC, for gas lift and injection in oil wells, gas turbine engines for power generation and jet engines, and on a smaller scale in fuel cell vehicles.
Most commonly, turbochargers are used in vehicles such as ships, heavy goods vehicles, and both large and small passenger vehicles. There are numerous benefits to equipping a car with this system – most notably safety, energy efficiency, and fuel economy. Compared to a standard atmospheric counterpart, the power of a turbocharged engine can be doubled which ensures the car reacts more quickly and efficiently to the commands of its driver, thereby making it safer.
When gases leave the engine of a turbocharged engine, the energy generated by them is processed and transformed into power. This gives turbocharged vehicles increased fuel efficiency. Alongside this fuel efficiency, charged cars are also more energy efficient. Turbo compressors supply more air into an engine, resulting in greatly improved combustion in the cylinder chamber. This reduces the amount of nitrogen oxide and carbon dioxide produced, increasing the sustainable properties of charged cars as opposed to traditional vehicles.
What is turbo compressor surge?
Turbo compressor surge refers to aerodynamic instability within the compressor unit when the air pressure after the compressor is higher than the compressor itself can physically maintain. This condition causes the airflow in the compressor wheel to back up, build pressure and in some cases, cause compressor stall, a partial breakdown of the airflow through the compressor. A stall that results in the complete breakdown of the airflow is referred to as a compressor surge. The severity can range from a momentary power drop with little effect, up to a complete loss of compression and performance. In extreme cases of surge, the shaft bearings can be damaged due to the high loads generated and can even cause mechanical failure of the compressor wheel itself.
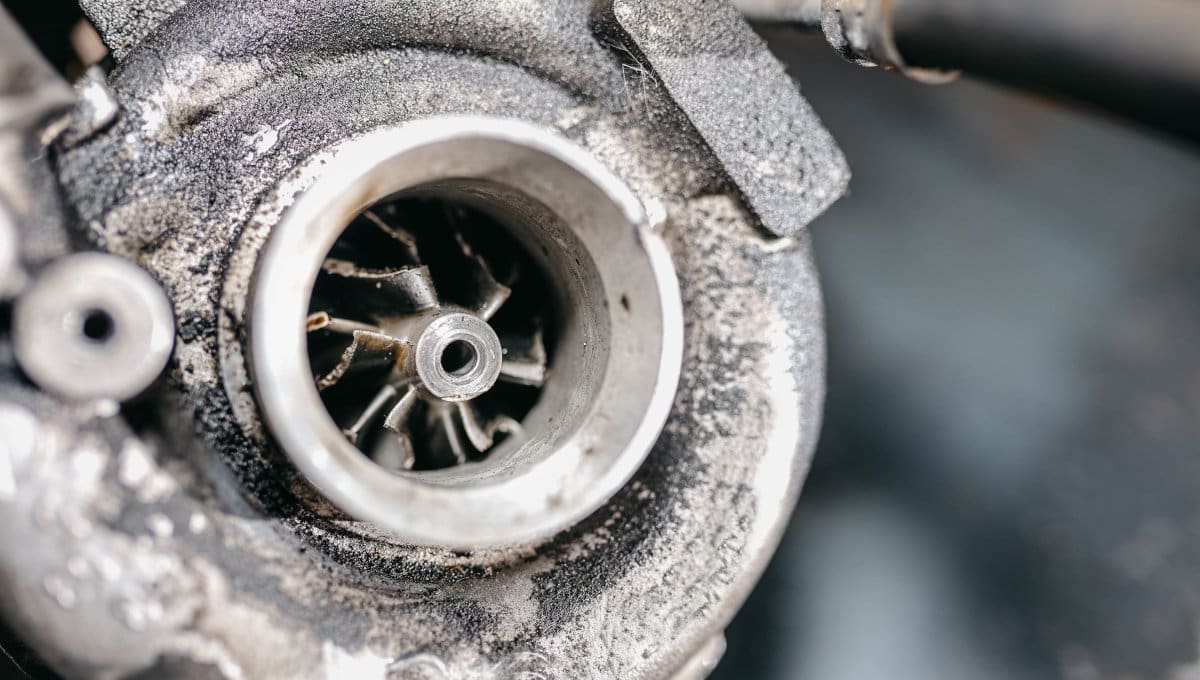
To help prevent surge, a pressure relief device called a Blow-Off (Bypass) valve is often installed on the air intake. If the throttle is closed rapidly, the airflow is suddenly reduced, causing airflow instability and pressure fluctuations. When this happens, the Blow-Off valve vents, relieving the pressure and helping to eliminate the occurrence of surge.