The manufacturing of tools and components is certainly not a new activity! Ever since human life evolved, mankind has been making things, from spear heads to spindles, wheels to widgets. The process used to make the objects or components, has been broadly speaking similar. Start with something larger and remove the bits you don’t need to make it into the smaller thing that you want. Flint reduced to axe heads; timber lathed into a spindle. This type of process is known as Reductive Manufacturing and has been the predominant technology for most of mankind’s history.
What is Additive Manufacturing?
Additive Manufacturing (AM), sometimes referred to as 3D printing or rapid prototyping, is simply the term used for manufacturing an object, by starting with nothing and incrementally adding layers of appropriate material until you build the thing you want. Whilst the concept of AM is not new, what brought about the increased focus on this way of manufacturing was the rise of the computer and the ability to control the manufacturing process digitally.
So called “3D Printing” brought the ability to turn a 3D Computer Aided Design (CAD) drawing into a physical object, at the push of a button. Rapid Prototyping was born, with engineers being able to create a physical prototype of a component, far more quickly than ever before.
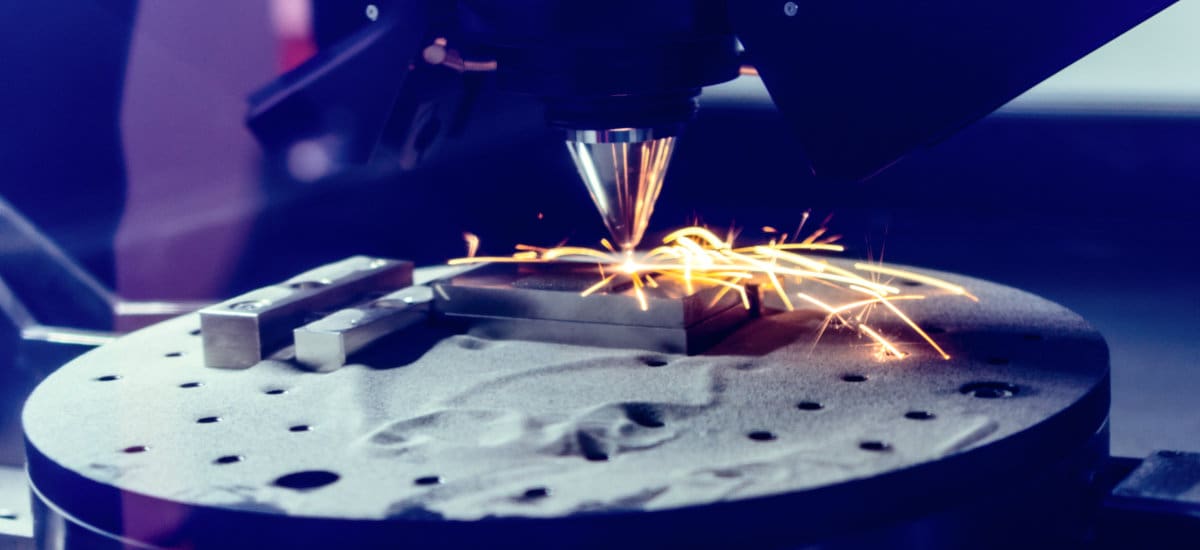
History of Additive Manufacturing Processes
The early days – Stereolithography (SLA)
Despite the hype and media interest in ‘3D Printing’ over the last decade or so, additive manufacturing (AM) is not new. The first patent for Rapid Prototyping was unsuccessfully filed back in 1980 by a Japanese Patent Lawyer. In 1984, a patent for Stereolithography (SLA), the use of targeted light to cause polymerizing resin to solidify, was filed in France. However, it wasn’t until 1987, when American Chuck Hill invented the first ever SLA machine. Creatively called SLA-1, the first 3D printer was born. Additive Manufacturing became a reality.
Fused Deposition Modelling (FDM)
In 1988, Scott and Lisa Crump invented a technology that controlled the 2-D extrusion of heated plastic onto a moving stage. A combination of the X-Y head movement and the Z stage movement, giving the full range of 3D motion required to make a solid object. Using a glue gun and a mixture of polythene and candle wax, Scott created a toy frog for his daughter. FDM is the process used by many modern 3D printers today, especially those associated with home and hobby use. Scott and Lisa Crump later went on to form Stratasys.
Selective Laser Sintering (SLS)
Stereolithography used light to set polymers and resins, Fused Deposition Modelling extruded plastics and some other materials. In 1992, the first Selective Laser Sintering (SLS) machine was unveiled to the world. This used a powerful laser to bond powered materials, including metals such as titanium, as well as glass, ceramics and indeed plastics. A thin layer of powder is spread across the printer bed by a roller, blade, or a brush seal (a potential new method, see below), and lasers used to selectively sinter the areas that are to remain solid. The bed is lowered slightly, a new layer of powder is applied and the process repeats. Unbonded powder is removed at the end of the process. Although far more flexible than Stereolithography, the use of lasers and powder makes the cost of Selective Laser Sintering higher. The need to carefully remove unbonded powder, also has an impact on the shape of the structures being created.
SLS Powder Scrapers
In many additive manufacturing facilities, rollers, blades or lips are used to distribute the powder where uniformity and flatness of the powder layer is of the highest importance. Brush seals are a potential new type of powder scraper which contains many thousands of fine wires.
Cross Manufacturing have pioneered the design, development and manufacture of brush seals for aerospace and power generation since 1976 where they have been used to form an effective barrier to gas flow or debris, whilst retaining the ability to deflect during excursions and thermal movements without permanent loss of sealing efficiency. Now these proven high tech seals could be applied to additive manufacturing for precise, uniform powder distribution to create Additive Manufacturing sealing strips.
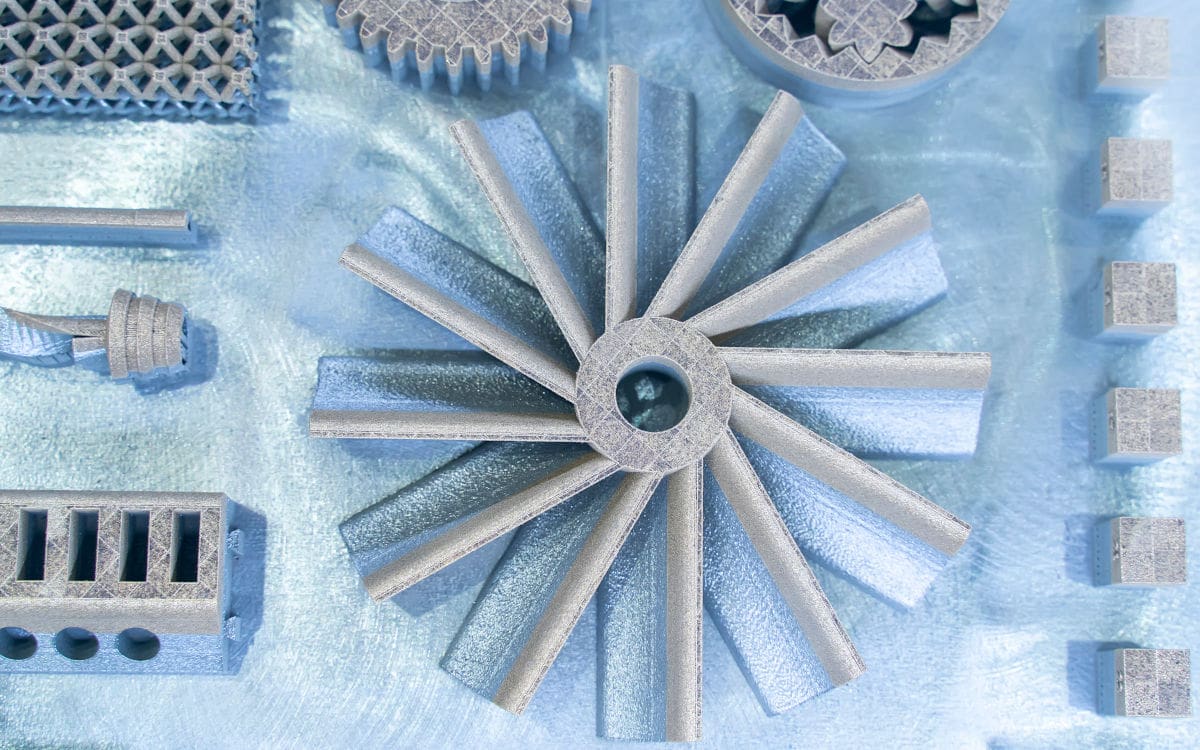
Additive Manufacturing Today
Because of the way the process works, the building of an object layer by layer, additive manufacturing is not a quick process. AM tends to be used where a low volume of high value parts are required, or where customisation is key. Spare parts for old cars are a great example. Rather than the need to store thousands of physical plastic components, the blueprints for each piece can be stored digitally and the part simply ‘printed’ to order.
The ability to take a virtual 3D CAD design and create it in the physical world, is a game changer. Combined with scanning technologies, it is possible to create bespoke components, matched to the patient’s anatomy and medical requirement. Already research is taking place on Bioprinting for liver transplantations.
The aerospace industry is widely using additive manufacturing. In 2015, Rolls Royce produced the largest ever civil aero engine component using 3D printing, the front bearing for a Trent XWB-97 engine. Made from titanium and 1.5 metres across, it contained 48 aerofoil-shaped vane components. Additive manufacturing is being used to create interior cabin components as well as jigs and tools used in the construction process.
NASA is also using additive manufacturing. Their DED 3D printing process produced one of the largest nozzles ever printed. Measuring over a metre diameter and nearly as tall, the nozzle, featuring fully integrated cooling channels, was fabricated in just under a month. By comparison, using traditional welding techniques, the device would have taken a whole year to produce.
What’s the future for Additive Manufacturing?
As additive manufacturing becomes mainstream, and the boundaries of the technologies are pushed, the possibilities for its use increase. No longer is the technology simply a tool for rapid prototyping, or indeed creating toy frogs! With increasing speed and accuracy, research into usage of new materials and the need for customisation, additive manufacturing is firmly set for a bright future.
New frontiers in the areas of food production and replacement organs are being developed. Entire houses have been constructed using giant 3D printers. And when mankind sets up a base on the moon or Mars, you can be sure that Additive Manufacturing will be at the heart of not only getting there, but also being used to sustain life in space.